Transforming Ideas into Reality: The Role of a Plastic Rapid Prototypes Factory
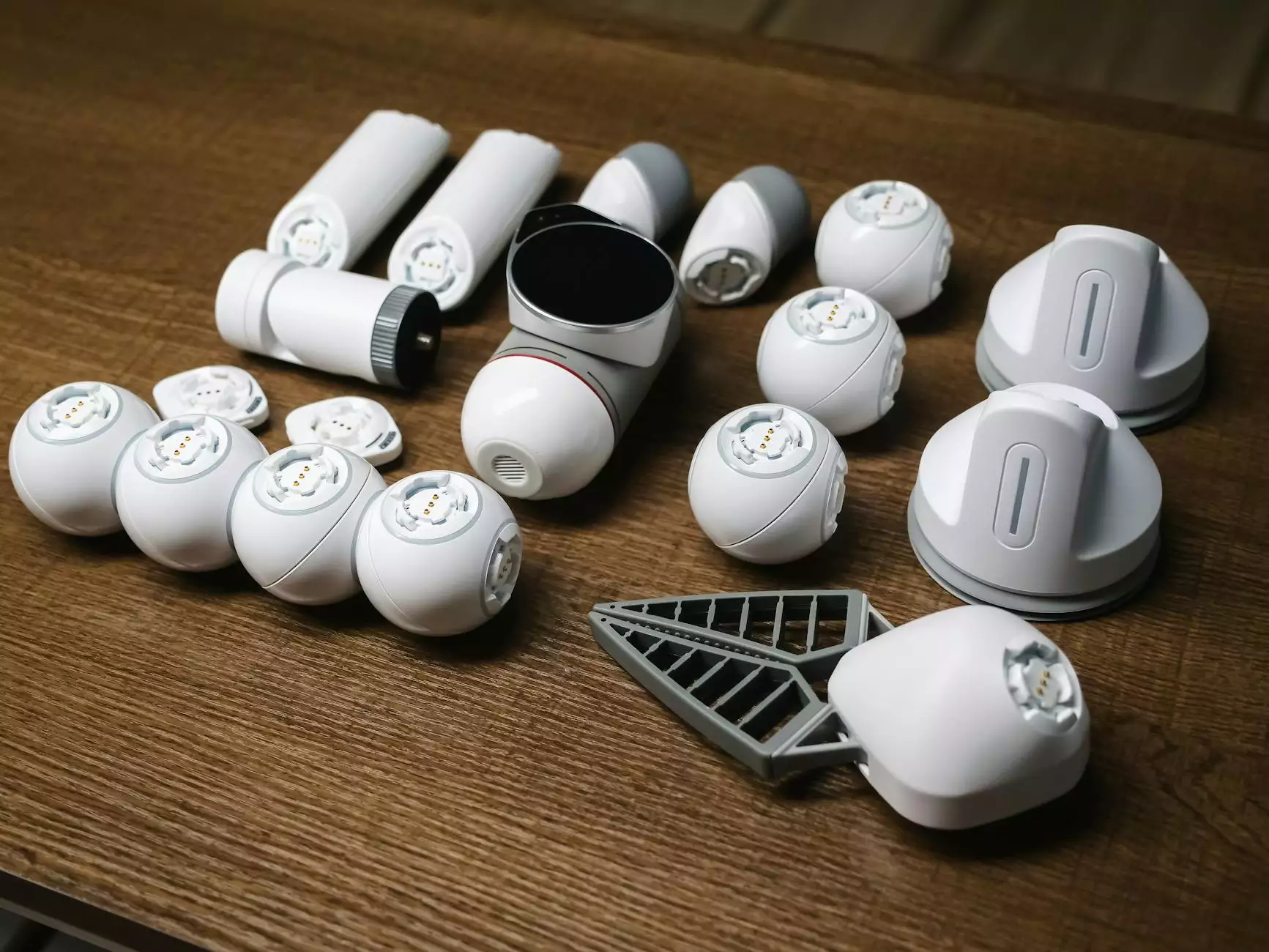
In today's fast-paced business environment, the ability to innovate rapidly is crucial for staying ahead of the competition. A plastic rapid prototypes factory serves as a vital partner for businesses seeking to bring their ideas to life swiftly and efficiently. This article explores the numerous advantages of utilizing a plastic rapid prototypes factory, the technologies involved, and how businesses can leverage this to enhance their product development processes.
The Importance of Prototyping in Product Development
Prototyping represents a crucial phase in the product development cycle. It allows businesses to test concepts and designs before full-scale manufacturing. Here are some key benefits of effective prototyping:
- Visualize Ideas: Prototypes help teams visualize the end product, making it easier to identify design flaws.
- Improve Collaboration: Prototypes facilitate better communication among stakeholders, from designers to engineers and marketers.
- Reduce Costs: Detecting issues at the prototyping stage minimizes costly alterations during production.
- Gather Feedback: Prototypes provide a tangible product for stakeholders to interact with, leading to insightful feedback.
What is a Plastic Rapid Prototypes Factory?
A plastic rapid prototypes factory specializes in the quick fabrication of prototype components using various plastic materials. These factories employ advanced manufacturing technologies like 3D printing, CNC machining, and injection molding to create prototypes that are both functional and representative of the final product. This capability stands out for several reasons:
Speed and Efficiency
The hallmark of a rapid prototypes factory is its ability to produce high-quality prototypes in a fraction of the time traditionally required. Shortened lead times help companies accelerate their development processes and respond to market demands effectively.
Cost-Effectiveness
Manufacturing a limited number of prototypes with precision can be expensive. However, facilities that specialize in rapid prototyping employ methods that significantly reduce costs related to materials and labor. This affordability allows businesses of all sizes to invest in high-quality prototypes.
Technologies Used in Plastic Rapid Prototyping
The plastic rapid prototypes factory utilizes several cutting-edge technologies to create prototypes efficiently. Below are some of the most prominent methods:
1. 3D Printing
3D printing is one of the most revolutionary technologies in prototyping. It involves additive manufacturing processes that layer materials to build objects from digital designs. This technology is widely enjoyed for its speed, flexibility, and low startup costs. Different types of 3D printing techniques used include:
- SLA (Stereolithography): Utilizes UV light to cure resin layer by layer.
- SLS (Selective Laser Sintering): Melts powdered materials to create a solid structure.
- FDM (Fused Deposition Modeling): Extrudes melted thermoplastic to form layers.
2. CNC Machining
CNC (Computer Numerical Control) machining is another prevalent method used in rapid prototyping. It involves the use of computer-controlled machines to cut, mill, or drill materials with precision. This method is particularly effective for creating intricate designs with tight tolerances and high-quality finishes.
3. Injection Molding
While injection molding is typically used for high-volume production, it can serve prototyping purposes, especially when multiple units are needed. This method entails injecting molten plastic into a mold, allowing for replicability in design while maintaining quality.
Applications of Rapid Prototyping in Various Industries
A plastic rapid prototypes factory serves a myriad of industries, enhancing product innovation and time-to-market. Below are some notable applications:
1. Automotive Industry
The automotive sector constantly pushes the limits of design and technology. Prototyping allows for:
- Testing aerodynamics for new car models.
- Prototyping complex parts like dashboards, trims, and exterior components.
- Validating innovative safety features before production.
2. Consumer Electronics
Consumer electronics evolve rapidly, necessitating constant innovation. Rapid prototyping aids in:
- Creating ergonomic design prototypes for easy usability.
- Rapidly developing and testing new product features.
- Enhancing design aesthetics and functionality through feedback.
3. Medical Devices
In the medical field, precision is paramount. Rapid prototyping is pivotal for:
- Developing custom tools and implants tailored to patient needs.
- Testing biocompatibility of new materials.
- Accelerating the approval process by creating functional models for clinical trials.
Choosing the Right Plastic Rapid Prototypes Factory
Selecting the right plastic rapid prototypes factory is essential for maximizing the benefits of rapid prototyping. Here are key factors to consider:
1. Expertise and Experience
Look for a factory with a proven track record in various prototyping technologies and industries. Experience ensures they understand the nuances of your project requirements.
2. Quality Assurance
High-quality prototypes are vital for accurate testing and feedback. Ensure the factory employs stringent quality control measures and uses high-quality materials.
3. Technological Capabilities
Evaluate the types of technologies the factory offers. A versatile facility with multiple prototyping methods can tailor solutions to your specific needs effectively.
4. Customer Support
Strong customer service enhances collaboration and addresses concerns promptly. Your chosen factory should provide guidance and assistance throughout the prototyping process.
Case Studies: Successful Prototyping Projects
To illustrate the impact of a plastic rapid prototypes factory, let's explore a couple of real-life case studies where rapid prototyping played a critical role in a project’s success.
1. Smart Home Device Development
A tech company developing a new smart home device required a rapid prototyping partner to accelerate their design process. The team produced multiple iterations of device prototypes using 3D printing technology. Collaborating closely with the factory allowed the designers to refine functionality based on physical testing, ultimately leading to a successful product launch.
2. Innovative Medical Tool
A medical device start-up aimed to create a unique surgical tool. With stringent medical standards to meet, they utilized CNC machining for their prototypes, enabling precise tolerances. The plastic rapid prototypes factory facilitated iterative testing, which proved invaluable in meeting regulatory requirements and ensuring patient safety.
Conclusion: Unlocking Potential with a Plastic Rapid Prototypes Factory
In an era where speed and efficiency dictate success, a plastic rapid prototypes factory becomes an indispensable asset for businesses aiming to innovate and expand their product lines. By leveraging modern prototyping technologies, companies can reduce time to market, optimize costs, and significantly enhance the overall quality of their products. Whether you are in the automotive industry, consumer electronics, or healthcare, embracing rapid prototyping positions your business at the forefront of innovation. To explore how rapid prototyping can transform your ideas into reality, consider engaging with a dedicated plastic rapid prototypes factory like DeepMould.net, where quality and innovation meet to create the future.